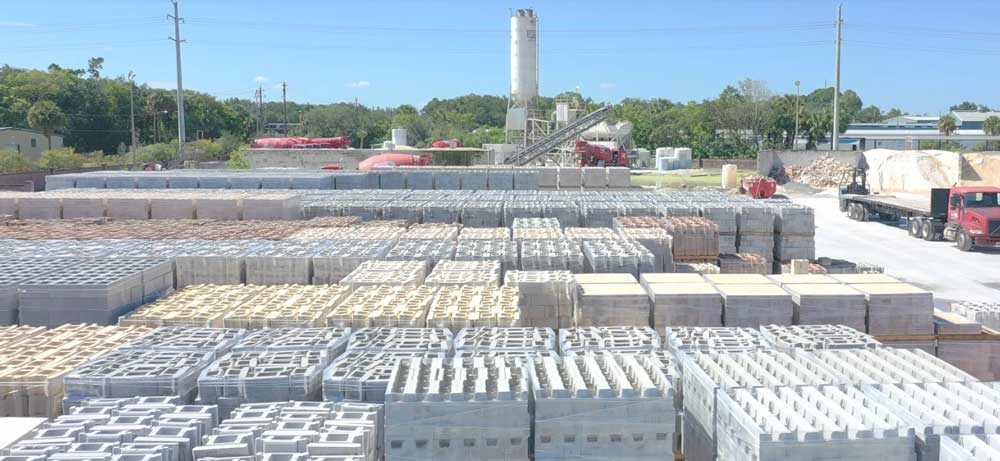
A-1 Block Corporation of Orlando will build and open a 55,000-square-foot concrete-block manufacturing plant on 25 acres just north of the County Fairgrounds off Sawgrass Road.
The Flagler County Planning Board approved the project’s site plan last week. The site was formerly residential and used to board horses. It is currently categorized as pastureland. It was rezoned. It is bordered by industrial land to the north. There are no residential parcels on Sawgrass anymore.
An 1,800-square foot residence will be converted into an office building. Four new buildings will be built: a 27,000-square-foot block manufacturing plant, a 15,000-square-foot machinery-repair shop, a 12,000-square-foot truck-repair facility, and a second 600-squerfoot office building. Several areas to the east of the plan will be devoted to block storage.
The site is connected to no utilities–no water, no sewer. It will draw its water from wells and discharge into septic tanks. Stormwater runoff will be collected and treated on site.
The buildings, Adam Mengel, the county’s planning director, said, will be “pushed to the east side of the site, so away from the roadway itself, away from Sawgrass, closer to the railroad tracks that are along the east side, hopefully in an area also where that’s not going to conflict with any activities we have going on the fairgrounds. That was one of our concerns with this.”
The manufacturing plant is in close proximity to the arena at the fairgrounds. Mengel said that the way the buildings will be situated, “those are going to be acting as a buffer. You also do have a landscape buffer that is proposed along the south boundary. Not much, but it’s enough to be able to hopefully provide at least some visual barrier that’s there.”
“We’ve tried to centralize the actual industrial use more toward the north side of the site,” Chris Ralph, the project engineer, told the planning board.
If the plant will generate noise that would be audible at the fairgrounds, “there are industrial performance standards, they have to meet those,” which includes noise standards, Mengel said. The company has not yet submitted building plans. Company officials could not be reached before this article initially published.
A-1 Block Corporation has been has been a family business for 65 years, according to its website, with eight operations in Central Florida. The Flagler County plant would follow additions in Sanford in 2018, Plant City in 2016 and Polk County in 2015.
Chris says
Better then more homes being built!
Joe D says
Well, the County citizens wanted business development that would not be residential, would expand the tax paying base, not be next to anyone’s home, not interfere too much with anyone’s sight line, bring in new (non-minimum wage) jobs, it’s going to get it’s own water supply from on-site wells, and deal with any run off internally…
There SHOULDN’T be much to complain about…pretty much ticks off ALL the boxes…but I’m sure SOMEONE will complain about SOME component(s) of the plan…just wait! It wouldn’t be Flagler County, if SOMEONE wasn’t UNHAPPY ….wait for it…
Where’s Flagler says
So what’s next for Flagler ? A medical waste transfer station with incinerator ?
Joe D says
And…there it is!!!
The COMPLAINT I predicted…only 2 hours ago!
BIG SURPRISE…with the hospitals and clinics in the area, where else do you expect Medical Waste treatment to be managed? If they place it near the block production company, it won’t be anywhere near local housing…another tax base benefit.
Medical Waste treatment plants are highly regulated, and generally don’t release anything back into the environment.
Billy says
Thats what they are making to block plant for! 75,000 new homes!
JonQPublik says
Not a bad idea entirely. Because of the risks, I’d imagine some of those jobs would be well paying.
Celia Pugliese says
Just some realistic research: https://emagazine.com/cement-plants-endanger-environment-human-health/#:~:text=Manufacturing%20plants%20release%20sulfur%20dioxide,with%20heart%20or%20lung%20disease.
Manufacturing plants release sulfur dioxide, nitrogen oxide (NOx) and carbon monoxide. Also, particulate matter, lead and mercury are produced from heating limestone, which is linked to worsening asthma, heart attacks and premature death in those with heart or lung disease, Also what about the water availability. Will their high demand for water use maybe in their own wells could dry up our Palm Coast utility wells? Was the to be affected city of Palm Coast consulted for this approval? Or they just do it like they did with the nuisance airport pilot schools which residents complains in the FIN airport X portal are well over 1000 since opened in July?
The dude says
It’s a start.
Good news indeed. We also need a good mix of technology to go with the industrial.
Denali says
This is a sign of a continued housing boom with thousands more houses. Why else would they move here?
FlaPharmTech_former says
Yippee…more blue collar jobs.
FLF says
Would be curious as to number of jobs, hourly and salary and starting pay. It would be great to see a company settle here and actually have payroll levels that allowed enough earnings to own a house here, not have wait for “affordable” rental housing.
Denali says
This is not a cement production facility. They will be manufacturing Concrete Masonry Units (CMU). The process will include the use of sand, various aggregates, water and cement (which was processed elsewhere). They basically mix concrete, cast it in molds, allow the mix to cure, often in a steam room, release the newly cast block from the mold and stack on a pallet for shipment. The biggest issue with these plants is usually noise; both from the vehicle activity and the shakers used to consolidate the mix in the molds. Again, this is not a cement plant.
Celia Pugliese says
Nothing close to any USA coast line will ever be affordable!. We all have to start from the bottom up. Not the other way around. Rent/buy way inland and start moving closer to coast as you save. Where can some expect to work in a manufacturing cement blocks plant and make enough to live in FB or Palm Coast, on the beach front or a short mile from it? Please all here be real! But ,we may get water shortage or contamination of our existing wells with the cement plant by products. Never mind the loaded trucks that we will have to dodge or negotiate loaded semis among us taking heavy products elsewhere when now we have less just arriving with loads for local work! Then we will have to pay for our teared asphalt in our roads as county and city are broke now , no reserves to repave them. Can all here imagine the amount of loaded semis we will have to deal around us traveling elsewhere? One winning idea from County Mengel!!
The dude says
If it pays a living wage, it’s “good job”.
Something like this could serve more than just Flagler Palm Coast given it’s vicinity to Orlando and J’Ville, and points in between.
The Sour Kraut says
The significant taxes this type of business will pay should actually help cover the cost of repairing some of our roads.
feddy says
Before talking about its business impact and potential jobs lets first see how many they will employ, nothing in the article mentions that. Depending on the size, a small plant would be operating with 18-25 people to large plant would be 25 to 40 including leads and management. Will they hire managers, or will they bring in their own? These questions need to be answered before we celebrate future jobs coming to our area. I have a few friends that work in this industry from set up, to training and operations and one of the plants is Cemex. These plants are not just built for no reason, these satellite sites are built for a specific task such as major construction such as bridge building, infrastructure then after it is no longer needed, they are sold off or just removed.